In the food and beverage industry, ensuring product quality and worker safety is paramount. Various processes involved in manufacturing—from raw material handling to packaging and waste management—often involve the use or generation of different gases. These gases, if leaked or unmanaged, can pose serious health, safety, and environmental risks, including toxicity, flammability, and contamination.
Our advanced fixed & portable gas detection solutions are specifically designed to monitor and detect hazardous gases at critical points throughout food & beverage production, helping to prevent accidents, maintain compliance, and safeguard both personnel and products.
Here are some of the key processes related to Food & beverages Industry
Raw Material Handling & Preparation
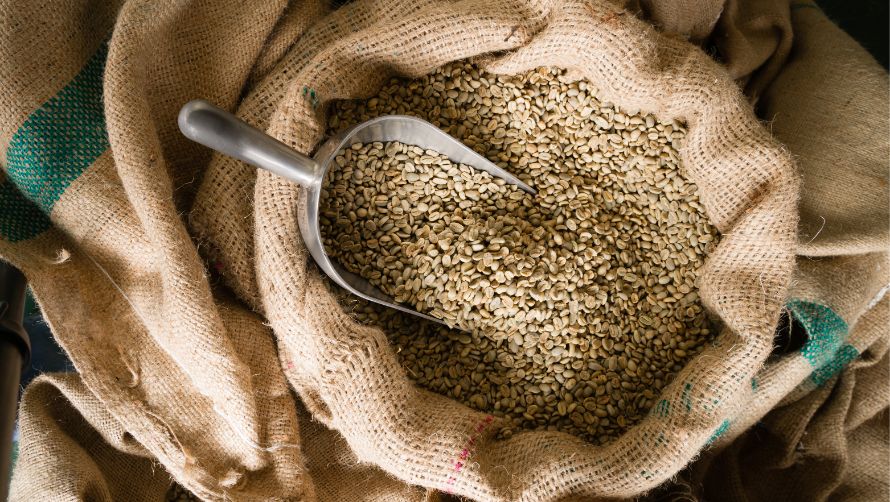
This stage involves the receipt, inspection, sorting, washing, grinding, and initial processing of raw food materials such as grains, fruits, vegetables, meat, and dairy. The purpose is to ensure that raw inputs are clean, safe, and ready for further processing or cooking.
Types of Gases Present
Carbon Dioxide (CO2) – May be released from fermentation-prone organic materials during initial handling or storage.
Ammonia (NH3)– Sometimes used in refrigeration systems near raw material storage areas.
Hydrogen Sulfide (H2S) – Can result from decomposition of organic matter in improperly ventilated areas.
Storage Silos / Raw Bins
Gases can build up inside sealed storage containers due to fermentation or decay.
Fixed Point Detectors: Near top and base of silos or raw bins.
Portable Detectors: During manual inspection or cleaning of bins.
Receiving Areas & Unloading Bays
Exposure to fumes from transported materials or refrigeration units.
Fixed Point Detectors: At breathing zone height along unloading docks.
Portable Detectors: During loading/unloading and truck inspections.
Thermal & Mechanical Processing
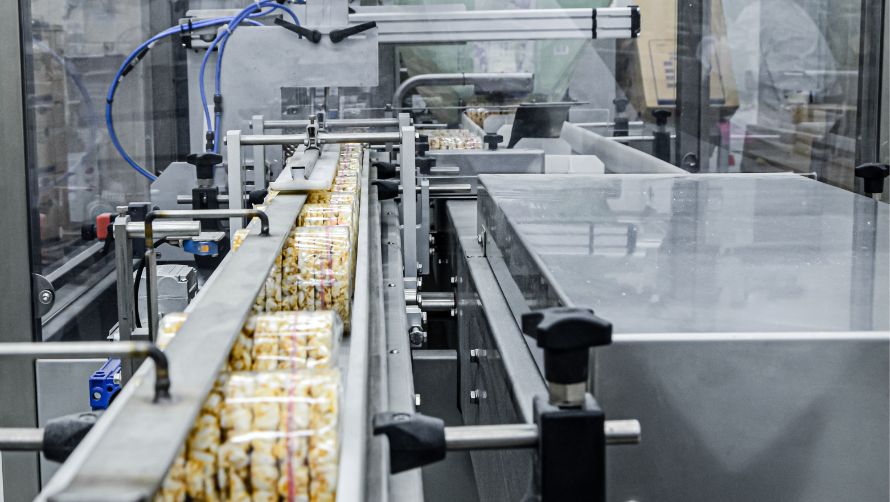
This includes operations like baking, frying, boiling, pasteurization, extrusion, grinding, blending, and other heat or mechanical treatments. These are critical for product safety, texture, and taste.
Types of Gases Present
Carbon Monoxide (CO)– Produced during incomplete combustion in boilers, ovens, and fryers.
Nitrogen Dioxide (NO2) – Emitted from high-temperature combustion or use of gas-powered equipment.
Combustible Gases (e.g., Methane, Propane, LPG) – Used as fuel for thermal processes and can leak from burners or supply lines.
Boilers and Burners
Leaks from fuel lines or incomplete combustion can release hazardous gases.
Fixed Point Detectors: Near combustion chambers and gas supply lines.
Portable Detectors: During maintenance and around joints or valves.
Cooking and Heating Chambers (Ovens/Fryers)
Risk of carbon monoxide or flammable gas buildup from faulty combustion.
Fixed Point Detectors: Just above ovens or fryers, near exhaust ducts.
Portable Detectors: When inspecting heating systems and ventilation performance.
Fermentation & Distillation
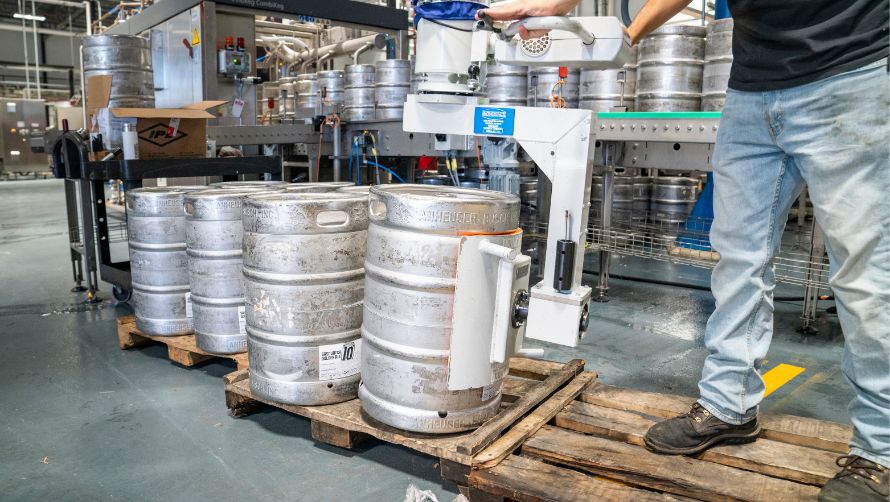
Fermentation is used in brewing, baking, dairy, and other processes to convert sugars into alcohol or acids using microbes. Distillation is applied to separate components, typically alcohol, through heating and condensation.
Types of Gases Present
Carbon Dioxide (CO2) – A natural by-product of fermentation.
Ethanol Vapors – Released during alcohol fermentation and distillation; flammable and potentially explosive.
Methane (CH4) – May be generated in anaerobic fermenters.
Fermentation Vessels
CO₂ buildup and ethanol vapors can leak from fermenters or storage.
Fixed Point Detectors: Above fermentation tanks and near venting/exhaust points.
Portable Detectors: During cleaning, maintenance, or sampling.
Distillation Columns & Condensers
Flammable ethanol vapors may leak from columns, seals, or transfer lines.
Fixed Point Detectors: Near column bases, condensers, and transfer piping
Portable Detectors: While checking seals, pumps, or during shutdown/start-up.
Refrigeration & Cold Storage
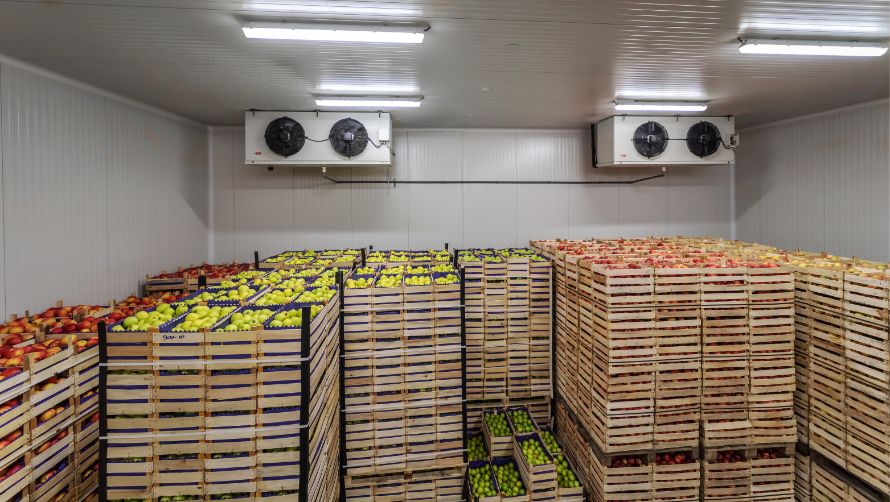
Used for preserving raw materials and finished goods, refrigeration and cold storage systems often involve ammonia, CO₂, or synthetic refrigerants to maintain low temperatures in processing or storage areas.
Types of Gases Present
Ammonia (NH3) – Common industrial refrigerant; toxic and corrosive.
Carbon Dioxide (CO2) – Used as a natural refrigerant.
Freon & Other HFCs – Used in smaller or packaged refrigeration systems; harmful in enclosed spaces.
Compressor Rooms & Chillers
Leaks from pressurized refrigerant lines or faulty valves.
Fixed Point Detectors: Around compressors, valve stations, and ventilation outlets.
Portable Detectors: During routine checks and leak investigations.
Cold Storage Chambers
Refrigerant leaks into enclosed storage areas pose inhalation risks.
Fixed Point Detectors: Near ceiling (for lighter gases like NH₃) or floor level (for CO₂).
Portable Detectors: Before entry into chambers or during servicing.
Cleaning & Sanitation (CIP/SIP)
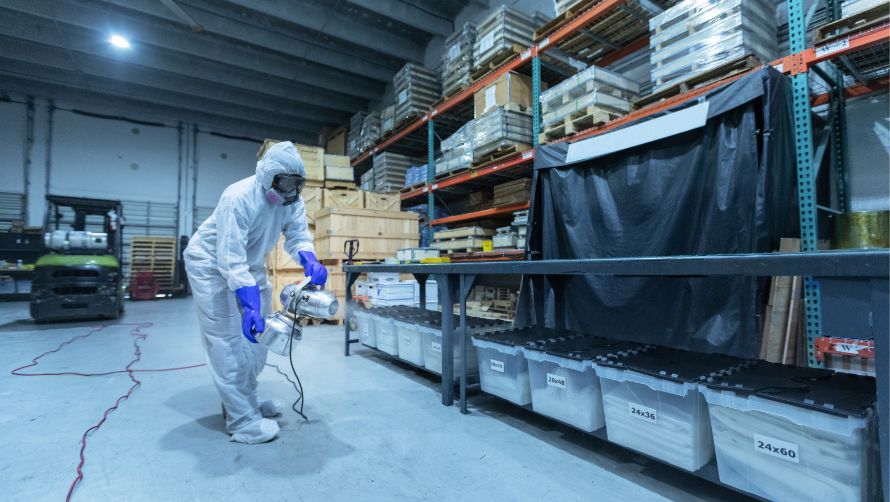
Clean-in-Place (CIP) and Steam-in-Place (SIP) systems clean equipment without dismantling, using chemicals, steam, and hot water. These processes are vital for hygiene and regulatory compliance.
Types of Gases Present
Carbon Dioxide (CO2) – From cleaning agents reacting with residues.
Chlorine (Cl2) – Used in some sanitation chemicals; toxic if inhaled.
Ozone (O3) – Used for disinfection in some advanced systems.
Chemical Mixing Stations
Risk of gas release from chemical spills or reactions.
Fixed Point Detectors: Near chemical tanks, dosing pumps, and mixing stations
Portable Detectors: During refilling, maintenance, and cleaning operations.
SIP Lines & Vents
Steam or gases vented improperly can lead to unsafe exposure.
Fixed Point Detectors: : At vent stacks and overhead areas near SIP headers.
Portable Detectors: During system activation and maintenance checks.
Packaging & Modified Atmosphere Packaging (MAP)
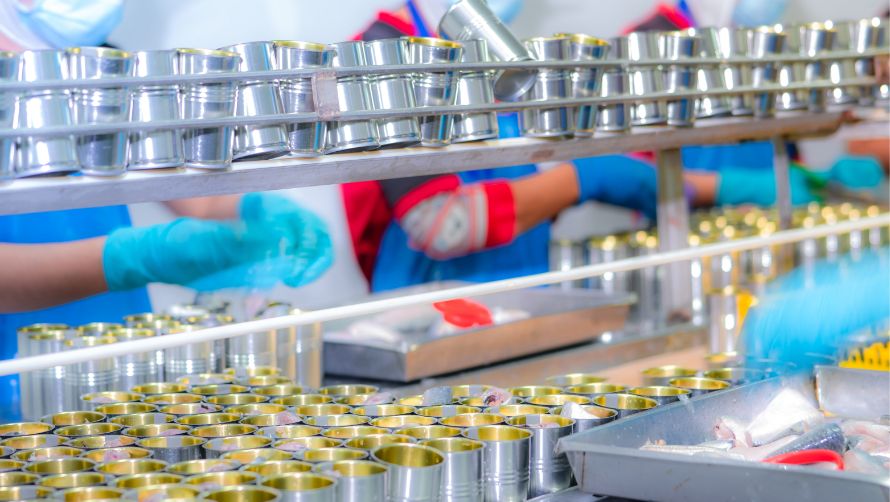
Involves sealing food products in containers or flexible films. MAP involves replacing air with a specific gas mix (CO₂, O₂, N₂) to prolong shelf life.
Types of Gases Present
Carbon Dioxide (CO2) – Common MAP gas; high levels can displace oxygen.
Nitrogen (N2) – Inert gas used for flushing oxygen; not toxic but displaces air.
Oxygen (O2)– May leak in high-purity MAP environments and lead to combustion hazards.
MAP Gas Injection Points
Leaks from nozzles, regulators, or hoses during gas flushing
Fixed Point Detectors: Around packaging lines and injection systems.
Portable Detectors: During gas cartridge replacement and leak tests.
Sealing & Packaging Machines
Residual gas may leak from improperly sealed packs or faulty seals.
Fixed Point Detectors: : Above sealing areas and around machine perimeters.
Portable Detectors: While inspecting seals or during line changeovers.
Additives & Mixing
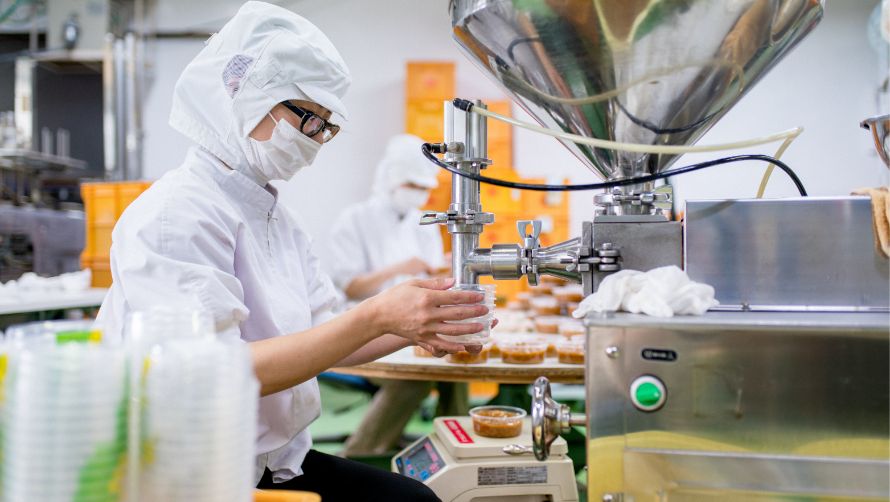
Food additives like flavorings, colorants, preservatives, and nutrients are blended into food via controlled mixing processes. These operations may involve powdered, liquid, or gas-based ingredients.
Types of Gases Present
Volatile Organic Compounds (VOCs) – From flavorings or solvents.
Dust or Gas Vapors – From powdered additives interacting with moisture or heat.
Nitrogen (N2) – May be used as a blanketing or mixing agent.
Ingredient Dispensing Stations
Risk of inhalation exposure from volatile or dusty materials.
Fixed Point Detectors: Near mixing heads, dispensing valves, and exhaust hoods.
Portable Detectors: During manual ingredient loading and cleaning.
Mixing Tanks & Vessels
Closed spaces can accumulate gases or vapors from additives.
Fixed Point Detectors: : On vessel tops and nearby air extraction points.
Portable Detectors: During tank entry, maintenance, or sampling.
Waste Handling & Biogas Recovery
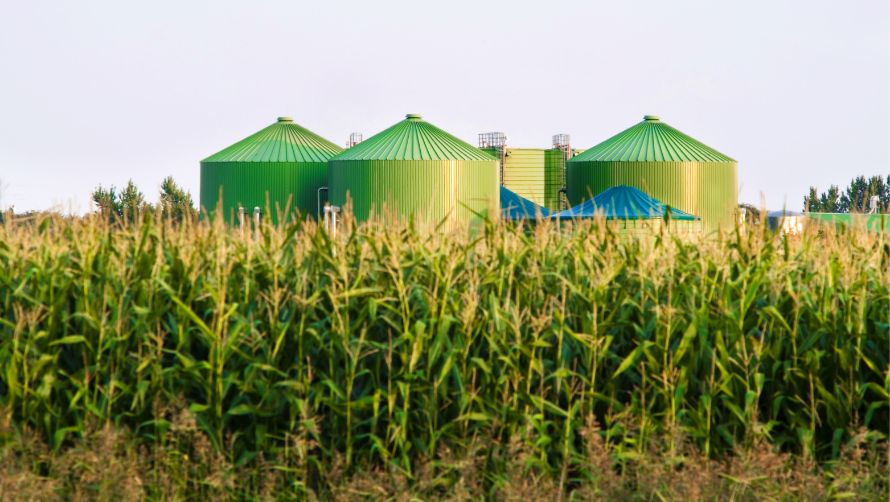
Wastewater, organic waste, and residues are treated or processed for disposal or energy recovery. Anaerobic digesters may be used to generate biogas from organic matter.
Types of Gases Present
Methane (CH4)– Produced during anaerobic digestion; flammable and explosive.
Hydrogen Sulfide (H2S)– Toxic gas from organic decomposition.
Ammonia (NH3)– Released from protein-rich waste materials.
Digesters and Gas Collection Units
Gases may leak from pressure vessels or piping systems
Fixed Point Detectors: Near digester tops, gas piping, and compressor outlets.
Portable Detectors: During inspections, pressure checks, or maintenance.
Wastewater Tanks & Sludge Areas
Gas buildup from stagnant organic matter or effluents.
Fixed Point Detectors: : Near tank inlets/outlets and confined access points.
Portable Detectors: Before tank entry or sludge removal.